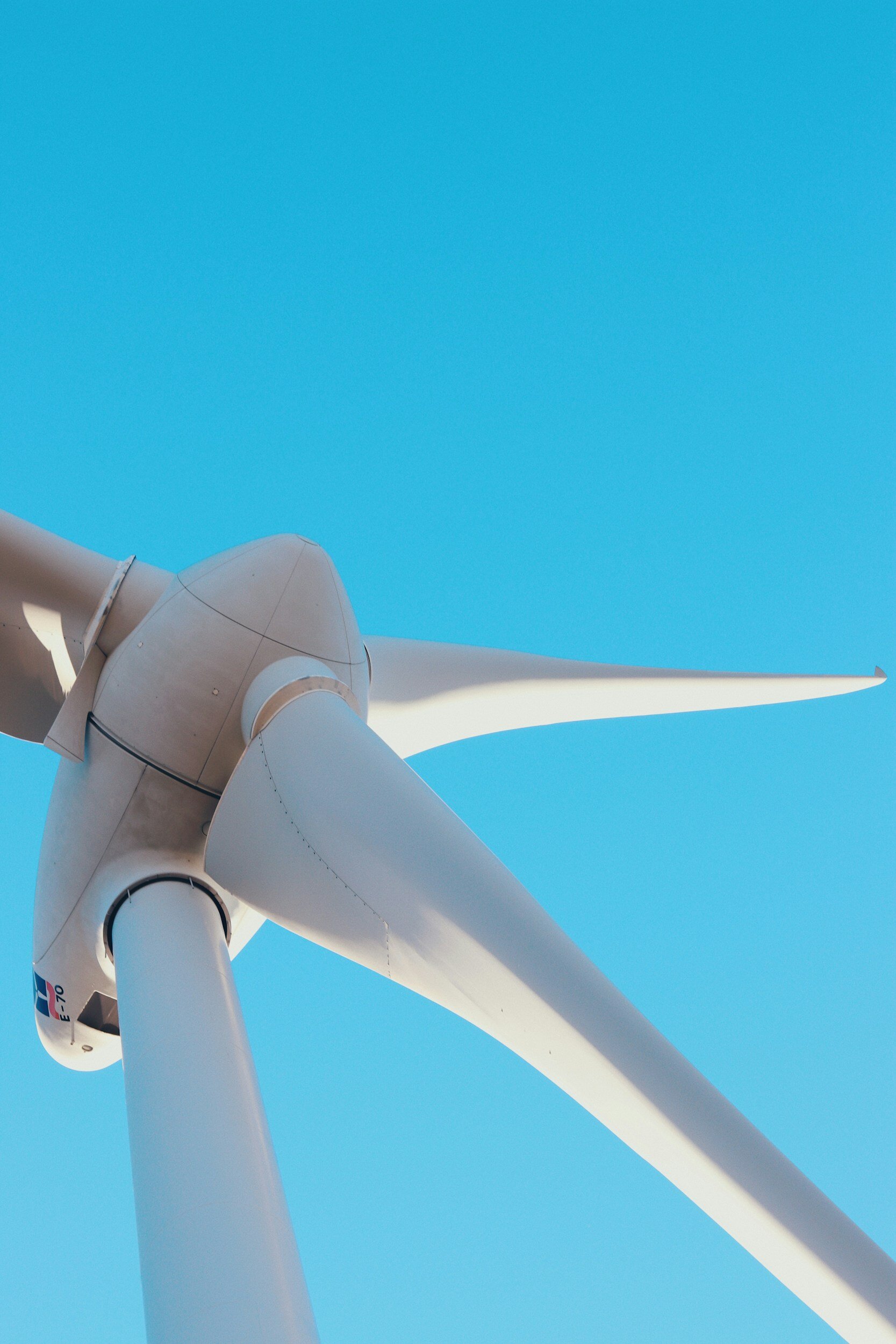
ENERCON GENERATOR SERVICES
At RFM Services, we employ a diverse array of techniques to offer asset owners and operators a comprehensive Generator assessment. Direct Drive Generators are particularly vulnerable to stator coil failures due to degradation stemming from moisture ingress and heat-induced breakdown of resin.
Generator assessments are essential for evaluating the status of your Generator. These assessments pinpoint any breakdown within the stator coils and the stator itself, providing an accurate evaluation of your Generator's condition. Our Generator assessment reports detail the current state, areas with heightened degradation, and recommend necessary corrective actions.
Regular Generator assessments conducted on your Direct Drive wind turbines can significantly reduce the likelihood of Generator coil failures.
PROVIDING ACTIONABLE INSIGHTS
>GENERATOR ASSESMENTS
After a Generator coil failure occurs, it is imperative to pinpoint the faulty coil or coils before proceeding with a coil bypass or replacement. An analysis conducted by the leading Direct Drive Wind Turbine manufacturer in the industry reveals that only 12% of Generator coil failures are detectable through visual inspections.
At RFM Services, we conduct thorough Insulation Resistance (IR) testing to precisely pinpoint the defective coil or coils. This process enables us to proceed with a coil bypass, single core repair, or replacement as needed. Our specialists in Direct Drive Generators boast extensive experience in troubleshooting all facets of Direct Drive Wind turbine Generators and hold qualifications equivalent to those at the manufacturer level.
RFM Services' Generator specialists provide tailored guidance to our clients on the optimal strategies to minimise asset downtime and production losses effectively.
MINIMISING ASSET DOWNTIME
>TROUBLESHOOTING
As Direct Drive wind turbines age, instances of Generator failure due to Phase to Earth or Phase to Phase faults are on the rise, underscoring the critical importance of effective Generator maintenance to mitigate the risk of failure.
It is recommended that Generator maintenance be conducted on Direct Drive wind turbines every 3 to 5 years, with the frequency depending on the moisture levels of the location. Regular Generator maintenance plays a pivotal role in averting Generator failures and the subsequent expenses and operational downtime.
A Generator maintenance procedure typically involves stripping away loose paintwork and resin from the Generator, addressing any corrosion, applying heat-resistant resin, and repainting the Generator.
Our Engineers employ industry-leading methods, such as dry ice pressure cleaning inspired by top wind turbine manufacturers, to deliver top-tier Generator maintenance services of the highest standard.
EXTENDING OPERATIONAL LIFE
>GENERATOR MAINTENANCE
Replacing Generator coils becomes necessary when coil failure leads to a Phase to Earth or a Phase-to-Phase fault. This process involves manually removing the faulty coil by dislodging individual cores, meticulously cleaning and re-insulating the surrounding area, and installing a new coil utilising a 1-2 tonne coil press. A typical coil replacement task can take anywhere between 15 to 20 working days to finalise.
On the other hand, Stator coil bridging is considered a temporary fix where the impaired coil is bypassed from the circuit to swiftly put the Generator back into operation. However, this bridging should not extend beyond a 30-day window as it significantly impacts production levels. Stator coil bridging usually requires 2 to 3 days to complete.
For minimal damages involving single cores that are accessible, a single wire repair can be carried out, limited to cases of up to 5 damaged cores. This repair process entails fixing individual cores and typically takes around 3 to 4 days to accomplish.
ENSURING THE CONTINUOUS OPERATION OF YOUR ASSETS
>COIL REPLACEMENT / BRIDGING
Direct Drive Generator pole shoes are highly vulnerable to failure due to a combination of factors such as resin breakdown, core degradation, and moisture ingress.
At RFM Services, we provide a range of services, including:
Troubleshooting: Extensive testing to pinpoint flawed pole shoes or temperature sensors.
Pole shoe replacement: Leveraging our strong partnerships with manufacturers enables us to locate and substitute faulty pole shoes.
Pole shoe bridging: Temporary operation at a reduced output through pole shoe bridging.
Pole shoe refurbishment: Our association with manufacturers grants us the ability to have your pole shoes refurbished by manufacturers.
PROVIDING TOP-TIER EXPERTISE
>POLE SHOE SERVICES
Moisture-related issues, such as moisture ingress, stand as the primary culprit behind coil failures in Direct Drive Generators. Generators situated in regions with high humidity levels face an approximately 80% higher likelihood of encountering Generator failures during their operational lifespan.
The efficient functioning of Direct Drive Generators relies on a constant flow of cool air to prevent overheating, where moisture naturally forms as a byproduct of the air-cooling process.
Although complete prevention of moisture entry into your Generator is unfeasible, you can substantially reduce its impact by incorporating moisture filters across the turbine.
RFM Services' Generator moisture retrofits encompass:
Yaw section filter retrofits
Cooling fan filter retrofits
Generator filter retrofits
Generator sealing and rain collar installation
De-humidifier installation
ENSURING ASSET INTEGRITY
>MOISTURE RETROFITS